What is a VRC?
A VRC (vertical reciprocating conveyor) is a cost-effective, safe and easy way to move materials from one elevation to another. With applications in a multitude of industries, these vertical conveyors offer an efficient way for warehouses, distribution centers, factories and other multi-leveled facilities to resolve their vertical material movement challenges. Due to their highly versatile nature, these vertical conveyors can easily be integrated with a building’s mezzanine, balcony, basement or any new or existing upper floor level. Comprised of a carriage, guide column and either a mechanical or hydraulic actuating mechanism (depending upon maximum vertical lift and capacity requirements), these vertical material lifts can be installed just about anywhere (inside or outside buildings, in unused elevator shafts, through floors, etc.). Gates and enclosures installed around the VRC shaft ensure the safety of personnel working around the lift. Carriage guarding and carriage gates protect materials on the lift during transportation between the various levels. Companies looking to make an investment in a solution that resolves their vertical material movement challenges should carefully consider these three vertical reciprocating conveyor benefits:Regulation
While elevators are designed to move both passengers and freight, VRCs are designed to move only freight. Due to this important cargo distinction, VRCs are in many jurisdictions exempt from strident elevator codes. Instead, these lifting devices are governed by their own national code that is administered by The American Society of Mechanical Engineers (ASME), one of the oldest standards-developing organizations in America. More specifically, vertical reciprocating conveyors must comply with ASME’s Safety Standard for Conveyor and Related Equipment (ASME B20.1-2018). This standard outlines the provisions for the construction, installation, operation and maintenance of conveyors and conveying systems. The goal of ASME B20.1-2018 is to ensure the safest possible operation of VRCs. However, this standard is far more relaxed than the regulations governing elevators. For VRC owners, this translates into less time spent ticking boxes on bureaucratic checklists (i.e. inspections, testing and routine maintenance programs) and more time spent on a company’s critical operational tasks. Warehouses and distribution centers that have routine material movement needs significantly benefit from the limited agency involvement that these vertical conveyors afford.Customization
A distinct advantage of VRCs is the degree to which they can be customized. Since elevators are designed to safely move human passengers, regulations have been put into place that restrict the size, capacity and lifting speed of these devices. While these safeguards are undeniably necessary for the safe transportation of people, these restrictions do not translate well for the fast-paced movement of materials and equipment in factories, warehouses and distribution centers. When moving more materials faster is the goal, a vertical reciprocating conveyor is needed. In deciding how to customize their vertical conveyor, customers will need to keep in mind the benefits and limitations of each type of lift. There are primarily two types of VRCs: hydraulic and mechanical. Hydraulic VRCs operate via a hydraulic pump/motor unit, actuating mechanisms and hydraulic cylinders that provide the force to move the carriage. Mechanical VRCs utilize a motor/gearbox with a drive shaft, bearings and sprockets that transfer the lifting power to a roller chain attached to the carriage platform. This type of lifting system is more suitable to larger loads, higher speeds and applications requiring more precise positioning. Additional differences between these two types of vertical conveyors are outlined in the chart below: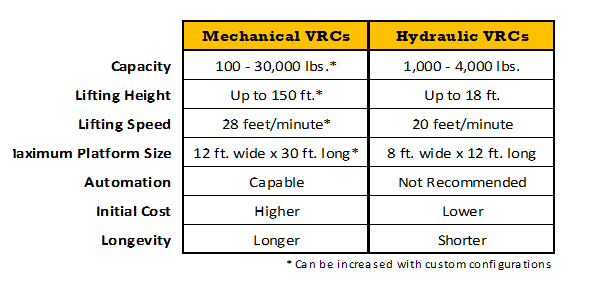