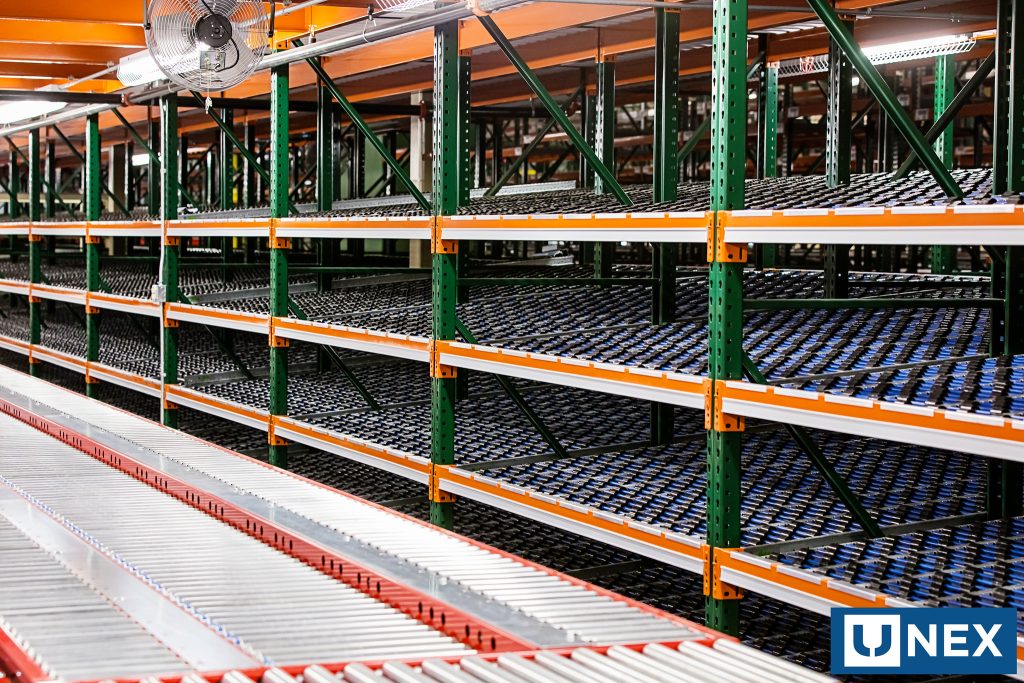
Conventional Solutions in the Order Picking Process
Finding seamless solutions can be tough as many managers tend to stick with the conventional route of pallet racking or shelving for basic storage and picking. Unfortunately, this is where the conversation stops as items are picked through racking and shelving units with little to no thought on if they are the best possible solutions for the job, especially when it comes to ergonomics. Ergonomic issues can occur as items in the back of racking can be hard to reach or even too high up for employees. These employees may need to over-extend into the backs or even reach in at awkward angles to pick the items, which over-time can cause back problems and other health/safety issues for these staff members. Organization issues can also occur as older parts left in the back or too high up may stay there leaving them to deteriorate or get lost in storage. Larger and small parts may not be stored properly creating an issue of inefficient storage thus taking up more space than they may require.Taking Order Picking to the Next Level with SpanTrack
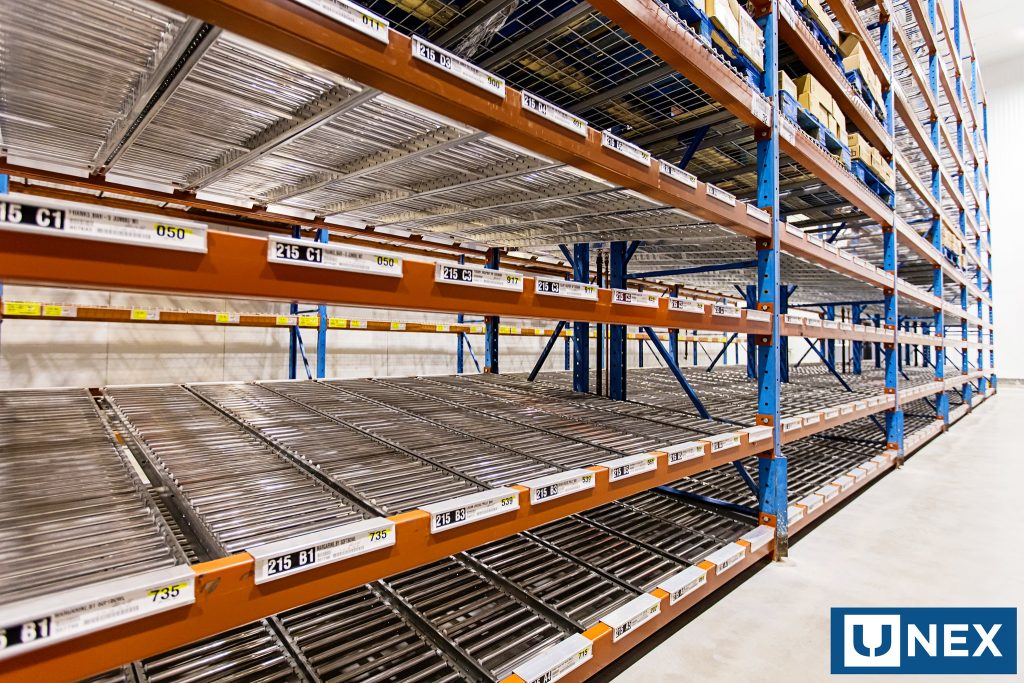
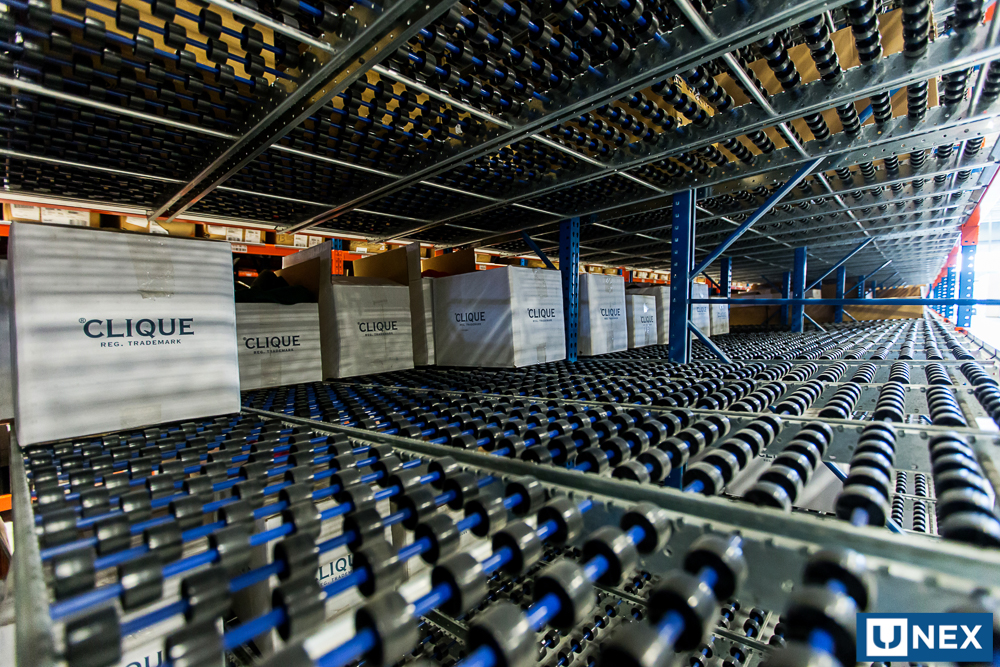
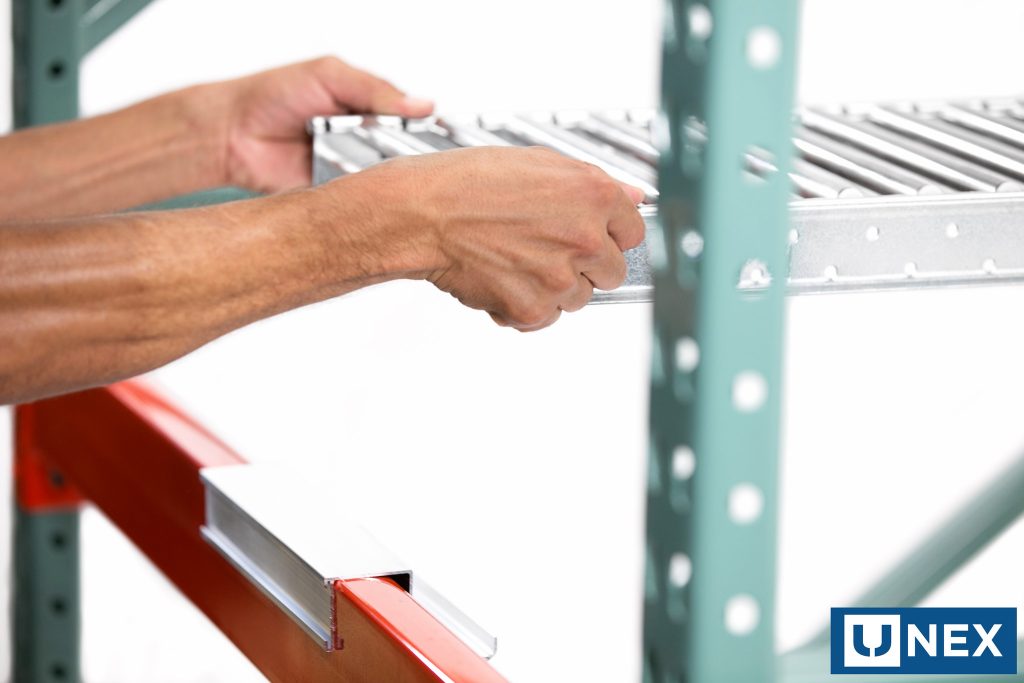