About the Client
This energy and utilites provider operates throughout large parts of New England. They have been around for decades and continue to this day, serving over 4 million customers.
They currently have over 30 office/facility locations and two headquarters: one in Boston, MA and one in Hartford, CT. As they continue to grow across New England, they are focusing on expanding into areas they do not yet serve.
Services include:
- Electricity Distribution
- Streetlight Implementation
- New Construction/Renovation Electrical Services
- Natural Gas Distribution
The Challenge
The client acquired three new buildings: one in Windsor Locks, Connecticut, one in Hyde Park, Massachusetts, and one in Wilmington, Massachusetts.
With this expansion came the need for an outfitting of the facilities’ racking, storage, and guarding solutions in all three locations. However, the distance between the facilities created logistical challenges, requiring careful coordination to ensure a smooth installation process.
Additionally, one of the facilities was a brand-new lease, which meant the necessary documentation for proper racking installation was not readily available. This added another layer of complexity to the project, requiring strategic problem-solving to ensure the job was completed efficiently and to the highest standards.
The Solution
BODE would have to coordinate projects at three different facilities in a timely manner, all while meeting deadlines for the client in order to get their facilities up and running as quickly as possible.
To overcome the logistical challenges of coordinating work across three separate locations, we relied on our dedicated team of project managers. Their expertise ensured that the planning and execution were seamless, allowing us to deliver a successful solution with minimal disruption to the client’s operations.
“This was a great project for BODE. We were able to coordinate 3 sites at the same time, that all presented their own unique challenges. It was important that our Project Management team work hand in hand with sales, to make sure all tasks were completed with a sense of urgency to stay on track. With 3 large scale projects in 2 different states, our team was able to work with multiple vendors to complete any necessary permit documents, including Life Safety/Egress Plans, Sprinkler Drawings/ Calculations, as well as the original racking layout design work. In the end, we were able to deliver on-time with a quick/seamless install to meet our customers expectations. “
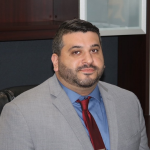
JJ Pereira
Outside Sales Representative, BODEFacility One:
Windsor Locks
The Windsor Locks facility was the newest and largest of the three. To address the challenges at the newly leased Windsor Locks facility, we brought in engineers to assess and sign off on the sprinkler system.
When installing pallet racking, it is essential to have a qualified professional verify that the racking is positioned correctly in relation to the sprinkler system. Proper clearance between sprinklers and racking ensures compliance with safety regulations and minimizes fire hazards. Once approved, our team proceeded with the installation of pallet racking, rack guarding, and shelving.
Click on a photo to view full-sized.
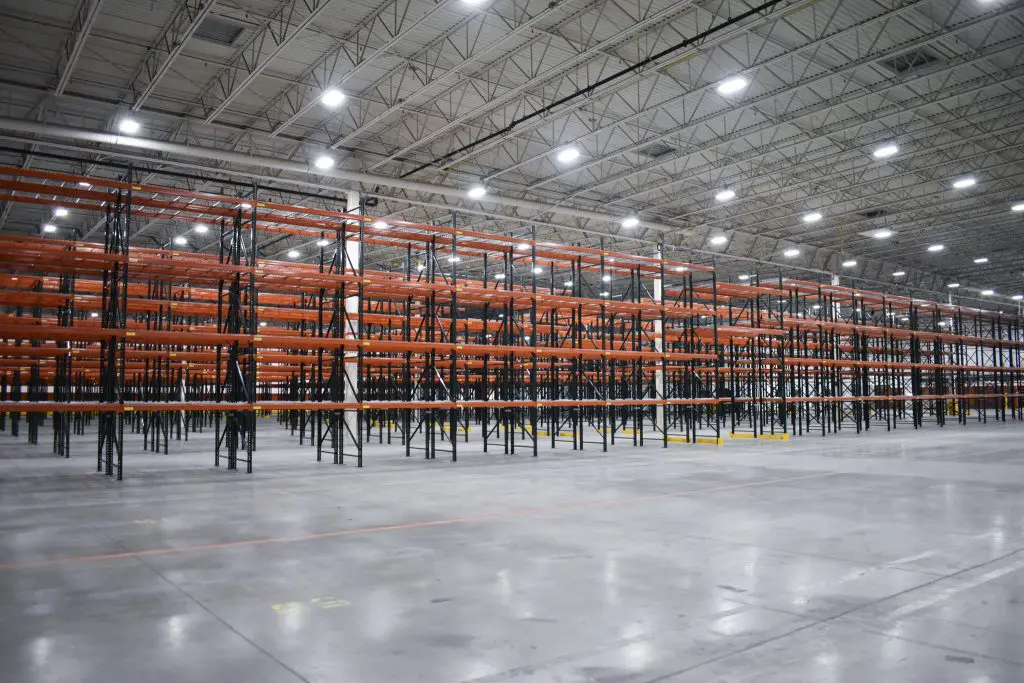
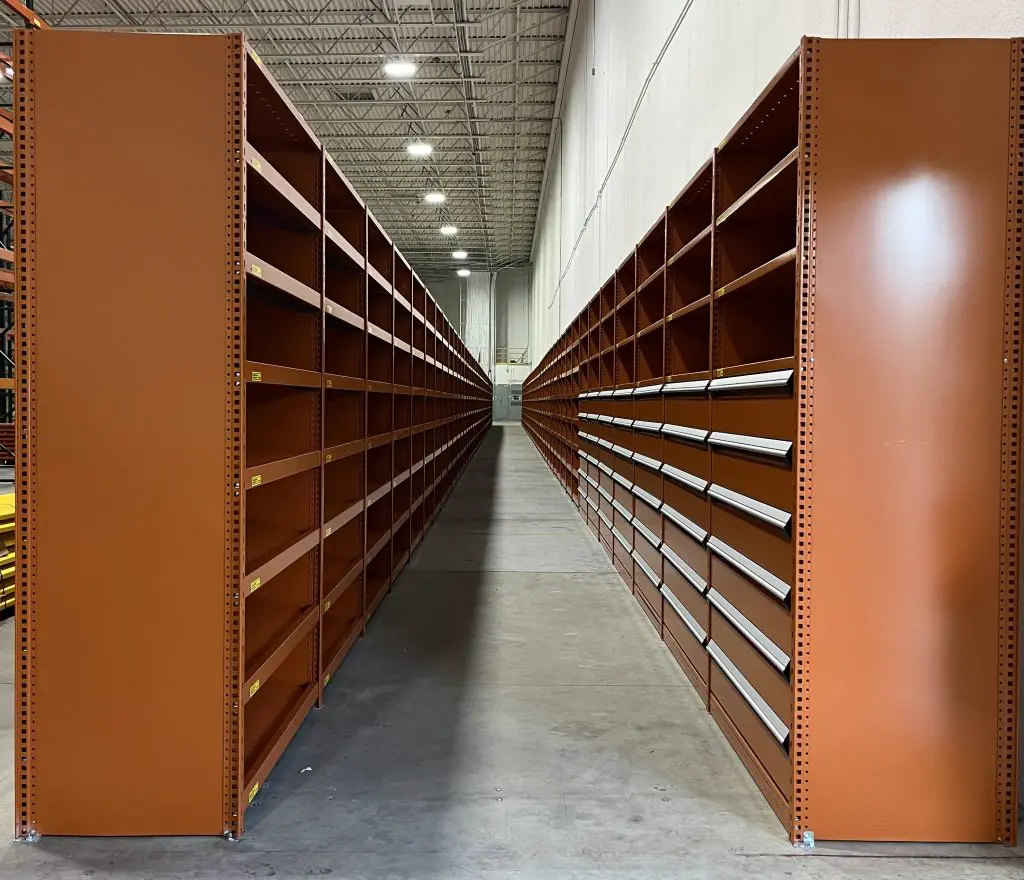
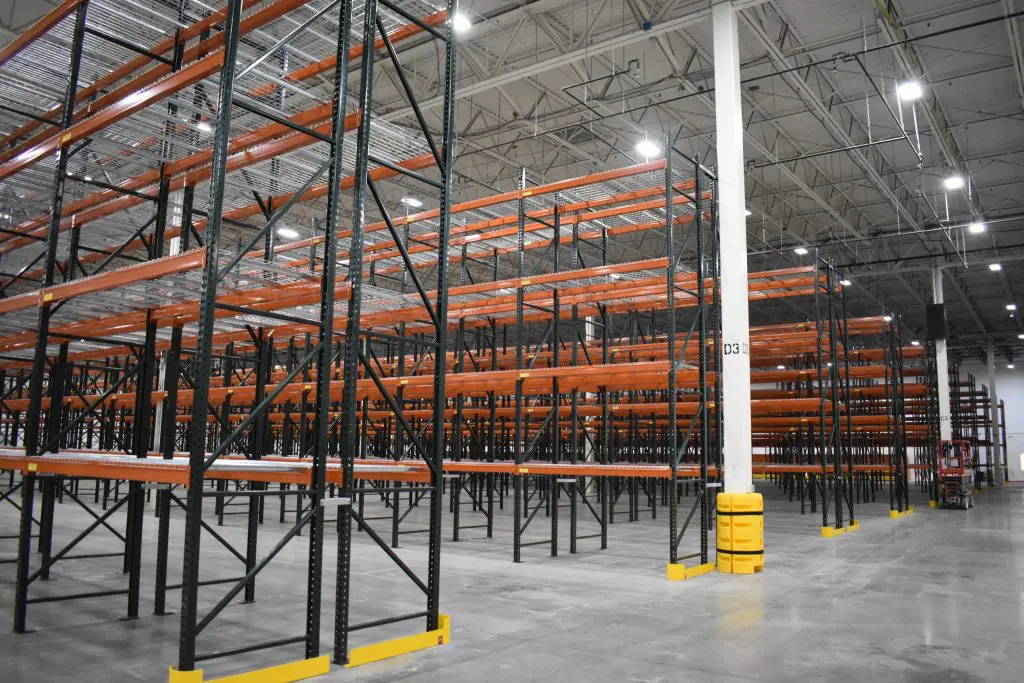
Facility Two:
Hyde Park
At the Hyde Park facility, additional safety measures were implemented by installing netting on the back of the pallet racking. This precaution helps prevent items from falling off the racks, reducing the risk of product damage and improving workplace safety.
Click on a photo to view full-sized.
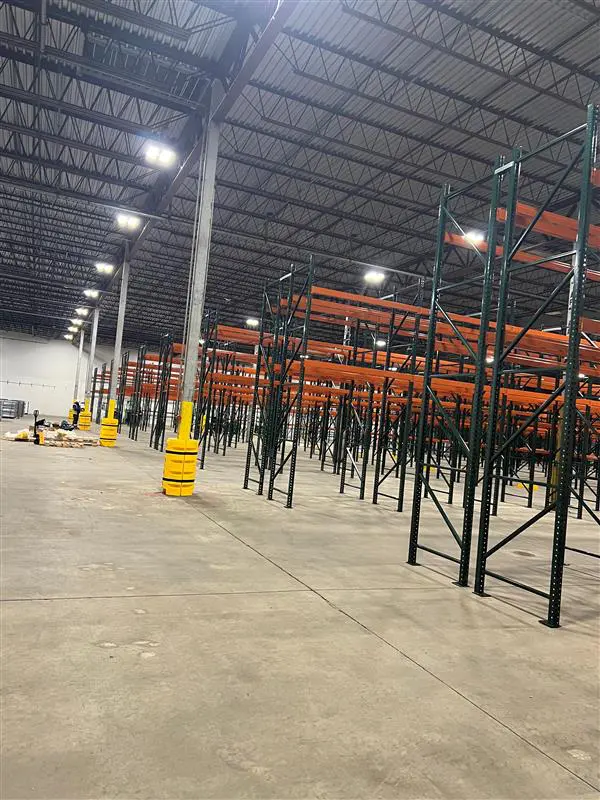
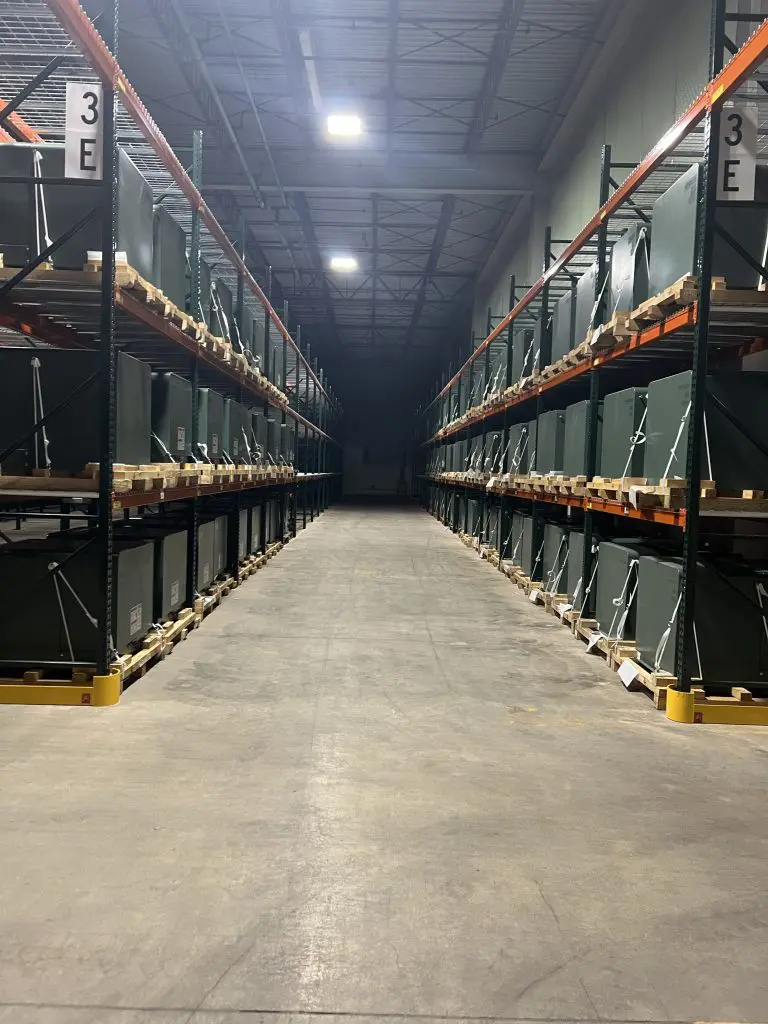
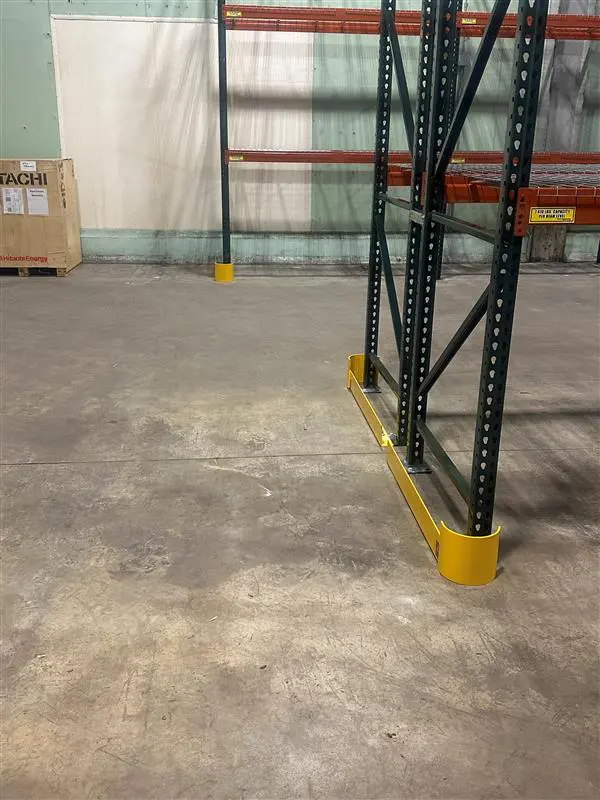
Facility Three:
Wilmington
Much of the same was done to the Wilmington facility, as all these projects required the same solutions and type of work. However, the Wilmington facility accommodated more in terms of guardrails to help protect wall systems and outline proper forklift paths.
Click on a photo to view full-sized.
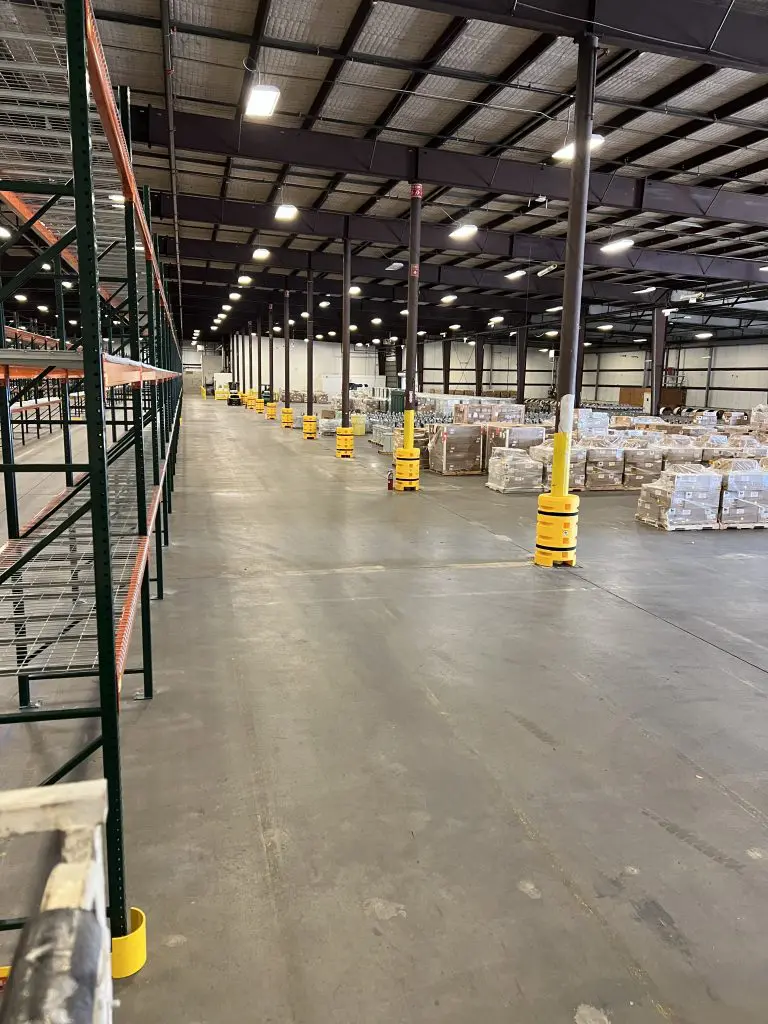
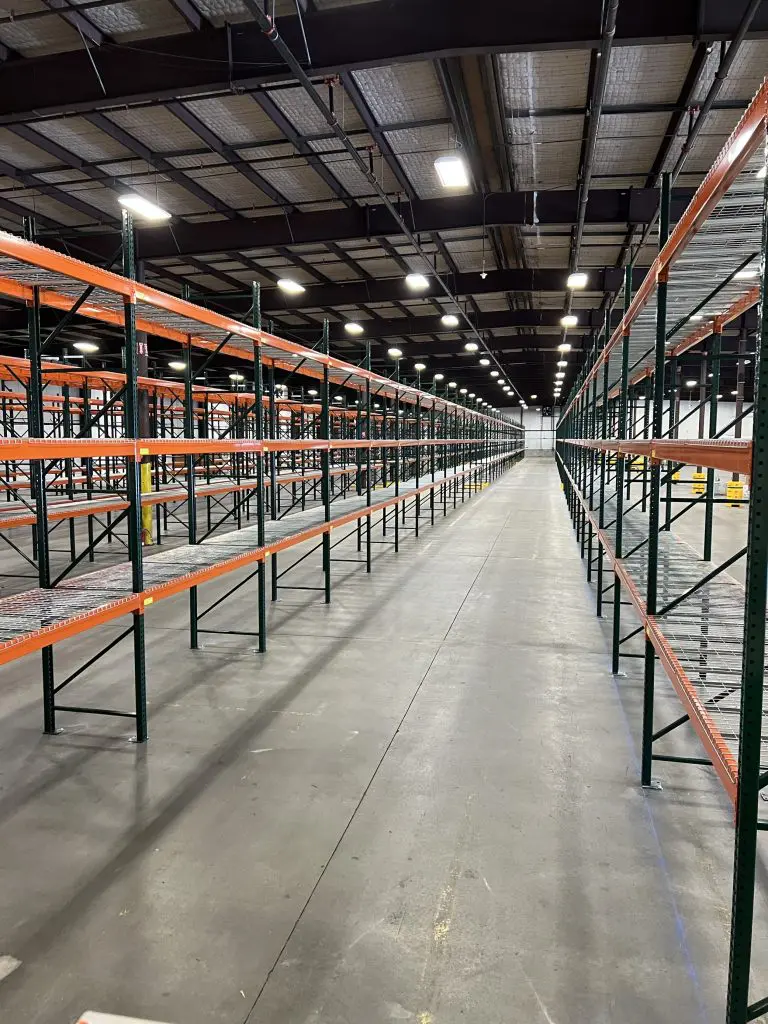
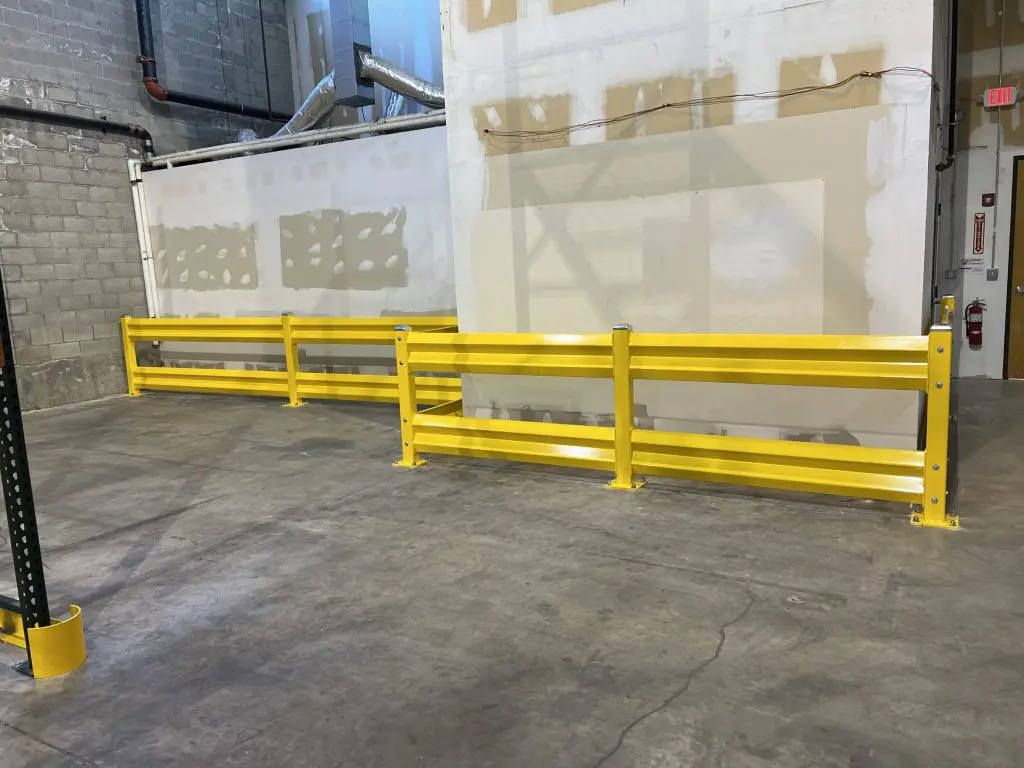
Conclusion
By carefully assessing each facility’s unique challenges and leveraging our team’s expertise, we successfully provided safe and efficient racking, guarding, and shelving solutions across all three locations. Through strategic planning and our dedicated project management team, we helped the client optimize their new facilities while ensuring compliance and safety.
“With JJ, Don Rose, Melissa, the install team, and me each handling our respective parts, we seamlessly worked through the project, making it a smooth process from start to finish.”
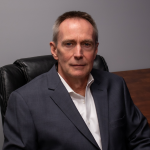
Bill Taylor
Project Manager, BODEMajor Products Selected
We chose industry-best products according to the specific needs of all three buildings.
- Pallet Racking
- Wire Decking
- Rack Guards
- Netting/RackBack
- Guardrail
- Shelving
- Modular Drawers