About the Client
Bayside Distributors, located in Brentwood, NH is a family owned company that was founded in 1948 in Newmarket, NH. They have been in business serving New Hampshire for over 60 years.
Bayside is a distributor and deliverer of beer, cider, hard seltzer, etc. in the Greater Seacoast and Southern New Hampshire area. They pride themselves on customer service and satisfaction, offering friendly sales personnel and quick deliveries.
A Returning Client to BODE
Bayside is an existing client for BODE. They have previously had work done by BODE back in 2023 consisting of Pallet racking and Wire Decks.
We enjoy being able to help our returning clients as it allows us to see how far they have come after implementing new solutions to their facility!
Case Study Video
Check out our YouTube video covering each step of the project below!
The Challenge
The client requested a 3,000 sq ft building for additional storage for their kegs, along with pallets of other products. The building was to have an open face for easy access.
BODE was hired for pre-construction services on this project. This required surveying the existing land, engineering a new site plan, and permitting through the town.
This project required a zoning variance due to the close proximity to the existing wetlands adjacent to the structure.
The Solution
BODE’s solution to this was to furnish and erect a Butler pre-engineered metal exterior structure, which included a BRII screw down roof, footings, asphalt, fencing, and any necessary permits. The building excludes walls, siding, and insulation.
The structure was designed to have an open front, enabling the easy access to the contents for Bayside employees that was requested.
The BODE team designed the building to fit within the existing impervious pavement on site. This solution allowed the team to move through the town permitting smoothly because of multiple factors:
- The building is more environmentally favorable because there is less salt/sand from winter conditions affecting the adjacent wetlands.
- The building was already in an existing impervious area. Therefore, the overall impact was not changing.
Pre-Construction Phase:
Initial Challenges
The BODE team faced some initial challenges in the duration of this project. The first was encountering unforeseen sub-surface conditions, including a ledge that needed to be hammered out in some areas before proceeding with excavation.
The crew also ran into organic subsurface materials that required us to overexcavate and fill with crushed stone, brought to the site.
Poor weather and low temperatures slowed the foundation and construction process; however, the BODE team was still able to complete the project on schedule!
Pre-Construction Phase:
Site Work
This phase contained all site work prior to the team breaking ground. This included Geotechnical consulting (Dig safe, test pit excavator, and observations, geotechnical report), structural and civil engineering services, planning board applications, and a Butler building preliminary.
The BODE team also had to receive approval for materials being used during this phase, such as concrete mix, rebar, and anchor bolts.
Click on a photo to view full-sized.
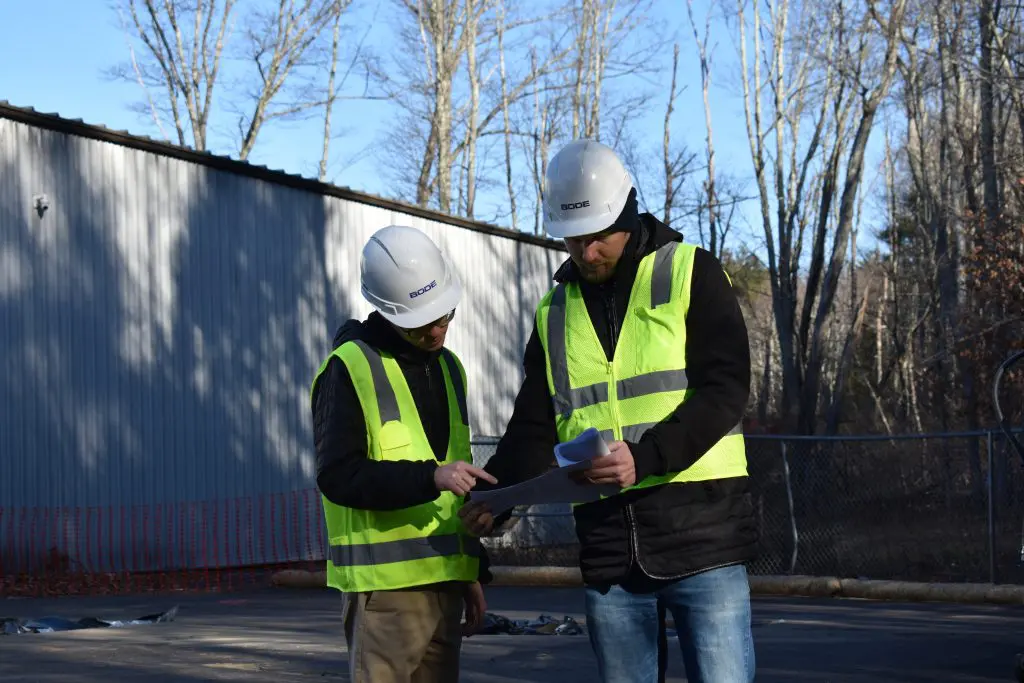
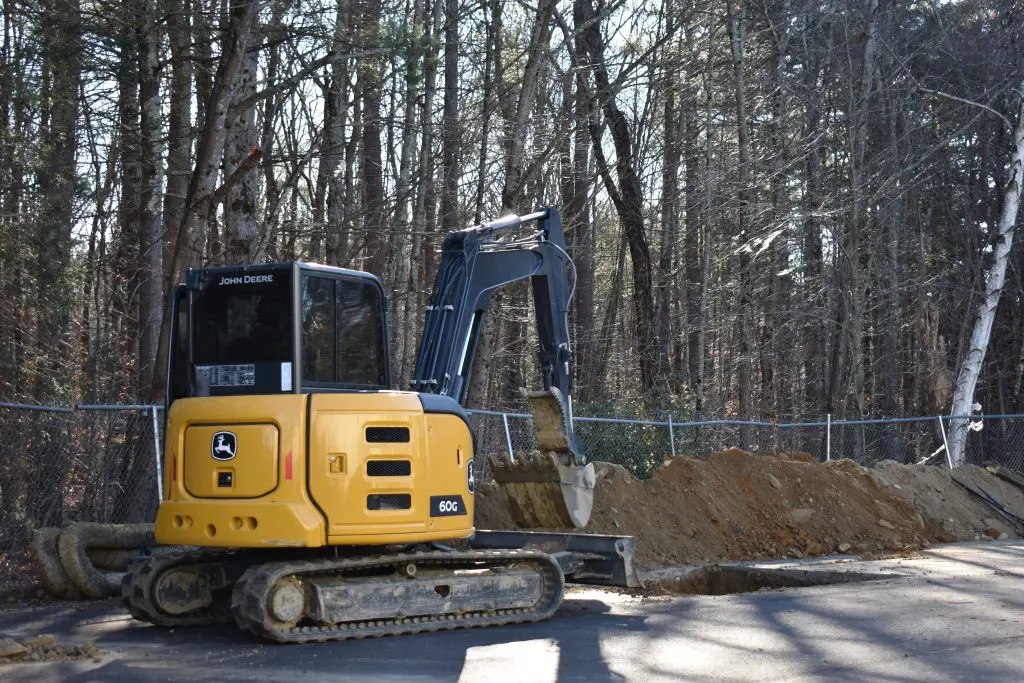
Construction Phase:
Mobilization
During this phase, the crew began to establish everything on site, such as building permits, temporary fencing, frost blankets, porta potty, and dumpsters. The crew was able to proceed with all necessary excavations.
During this process, many of the holes encountered groundwater, in which BODE had to overexcavate and fill with crushed stone. Soil samples were collected, and laboratory tests provided a compaction schedule for BODE to work with. The building structural grid was then staked out and prepared for the installation of all footings and piers.
Click on a photo to view full-sized.
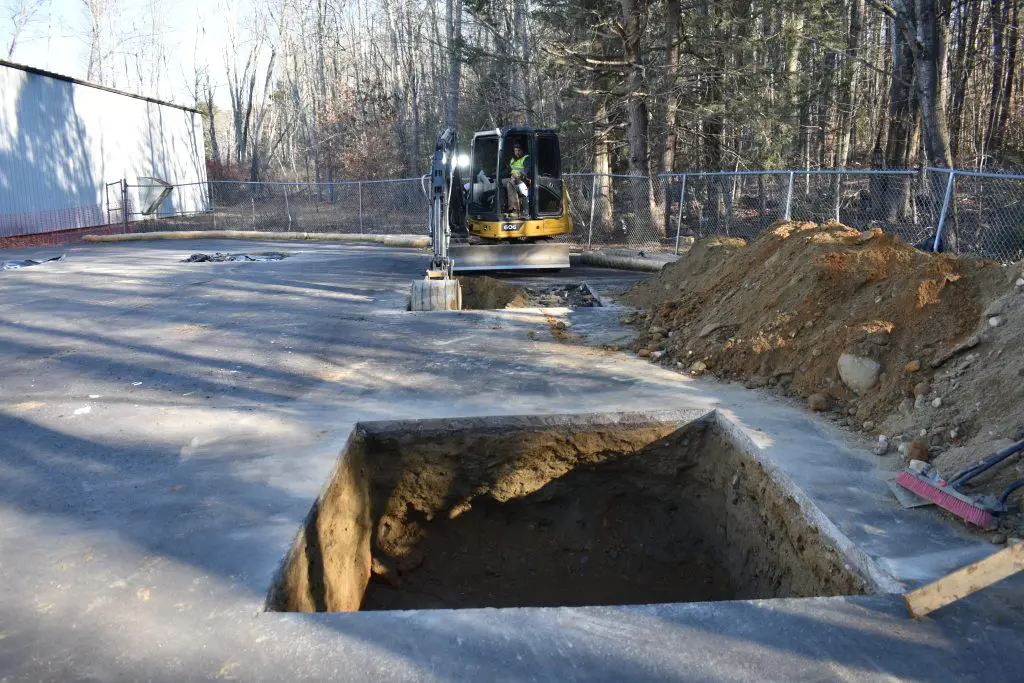
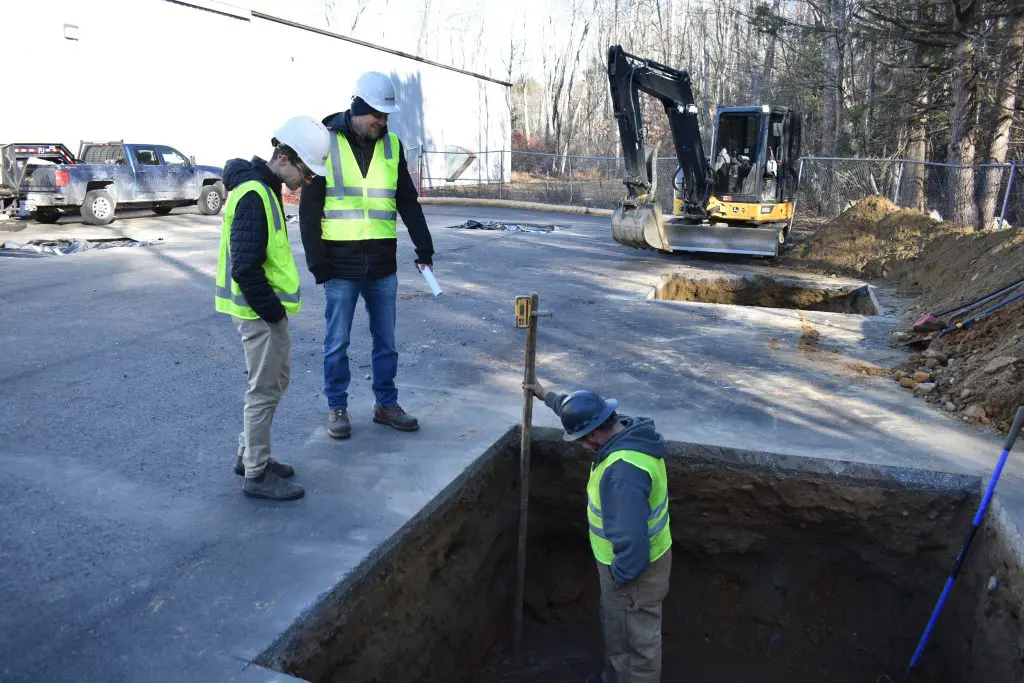
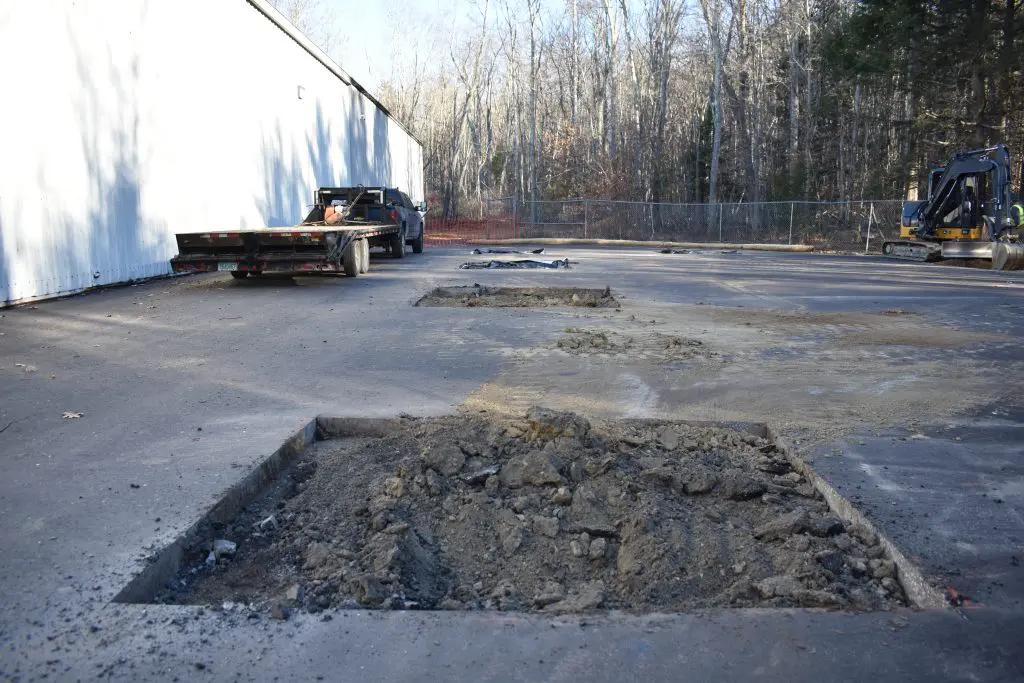
Construction Phase:
Primary Construction
Once the foundation footings and piers were poured, and the structural engineer reviewed and signed off on all concrete work performed, BODE could begin installation and construction.
Once the foundation footings and piers were poured, and the structural engineer reviewed and signed off on all concrete work performed, BODE could begin installation and construction.
Click on a photo to view full-sized.
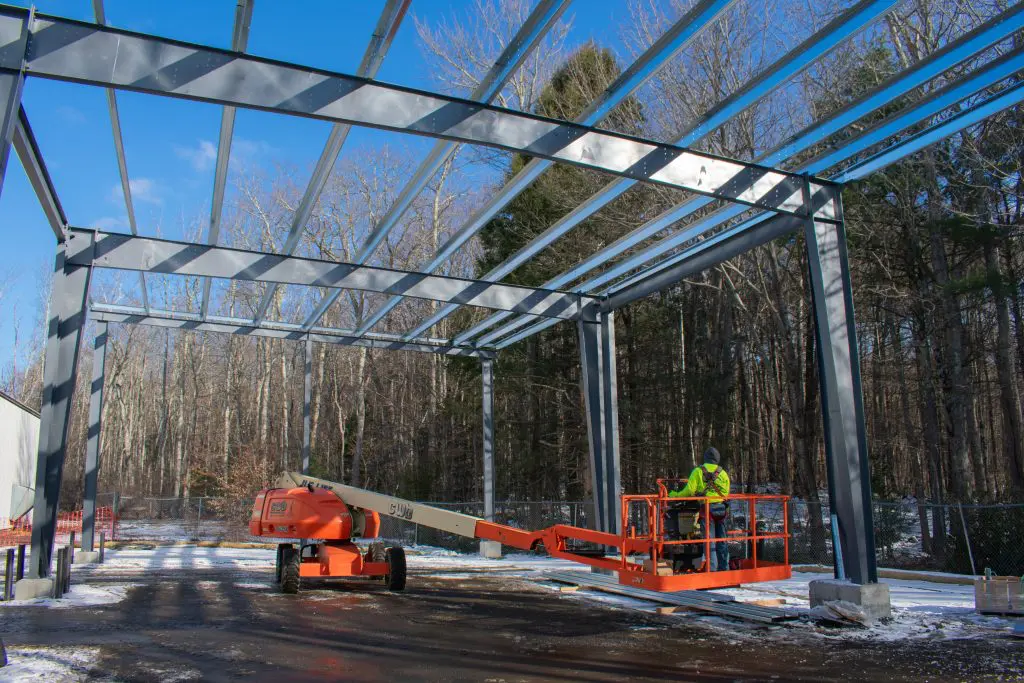
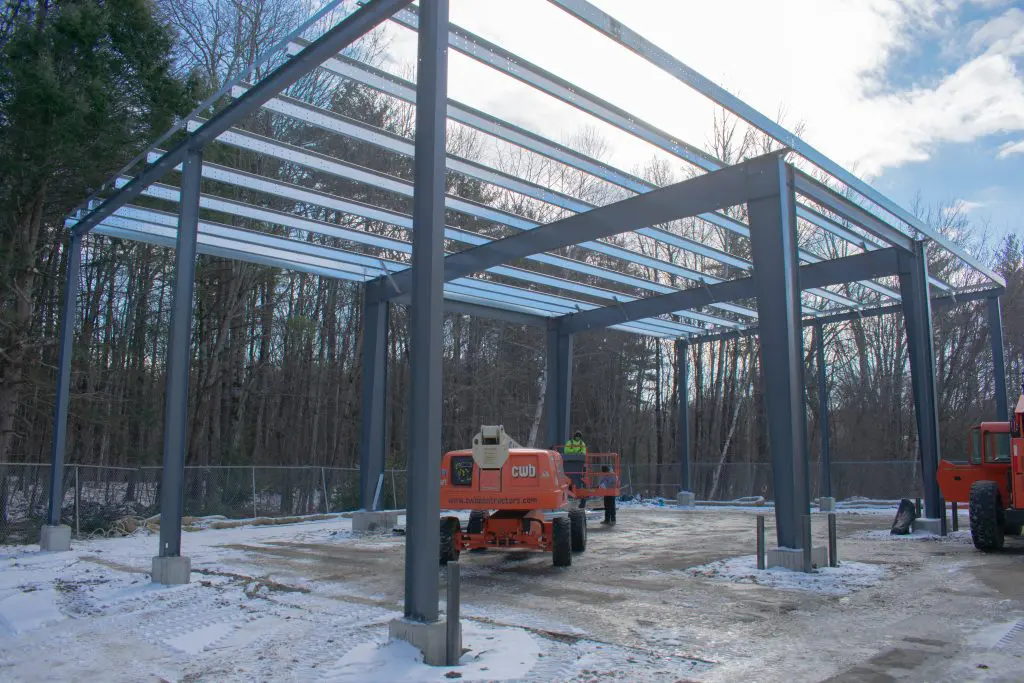
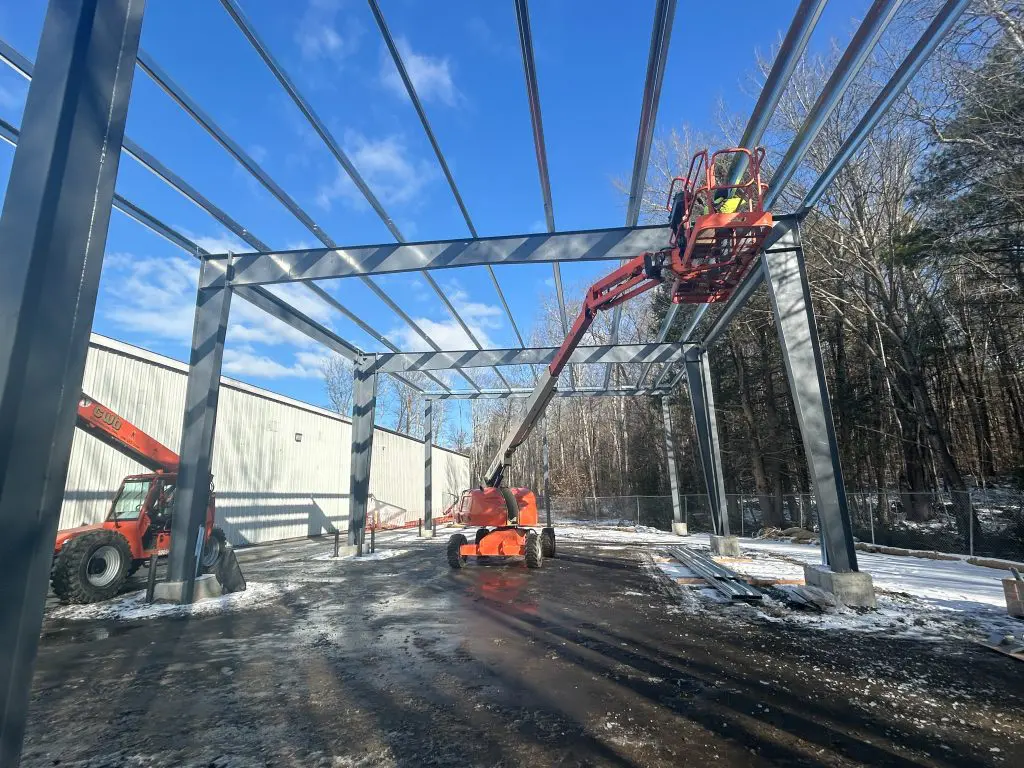
Construction Phase:
Final Construction
The BODE team faced some initial challenges in the duration of this project. The first was encountering unforeseen sub-surface conditions, including a ledge that needed to be hammered out in some areas before proceeding with excavation.
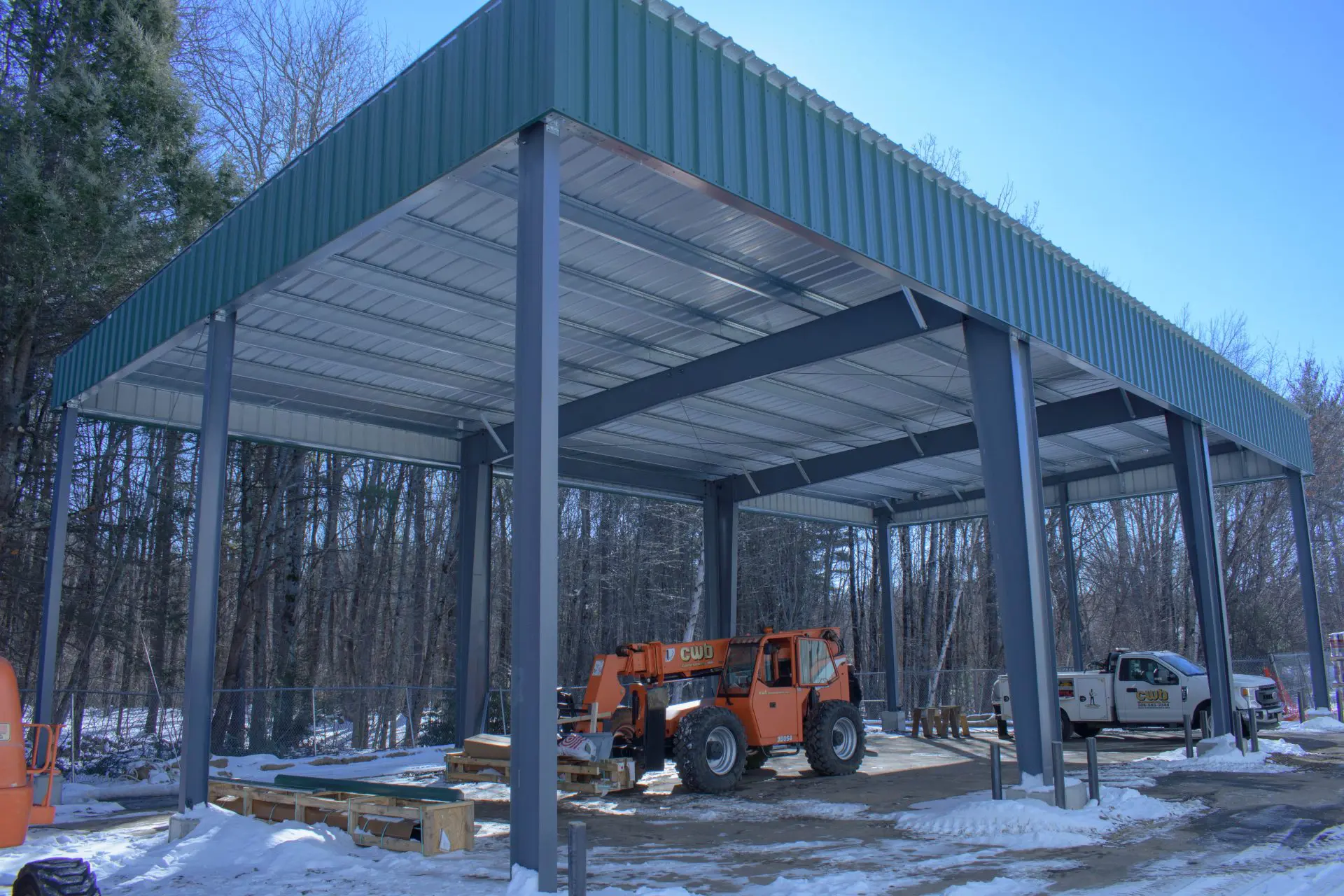
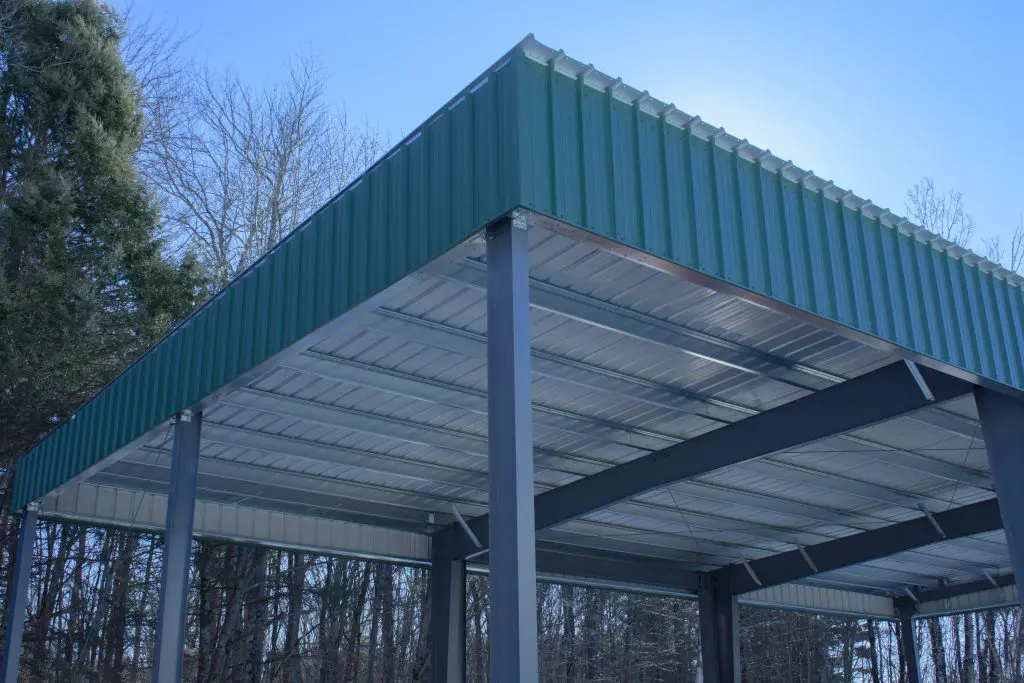
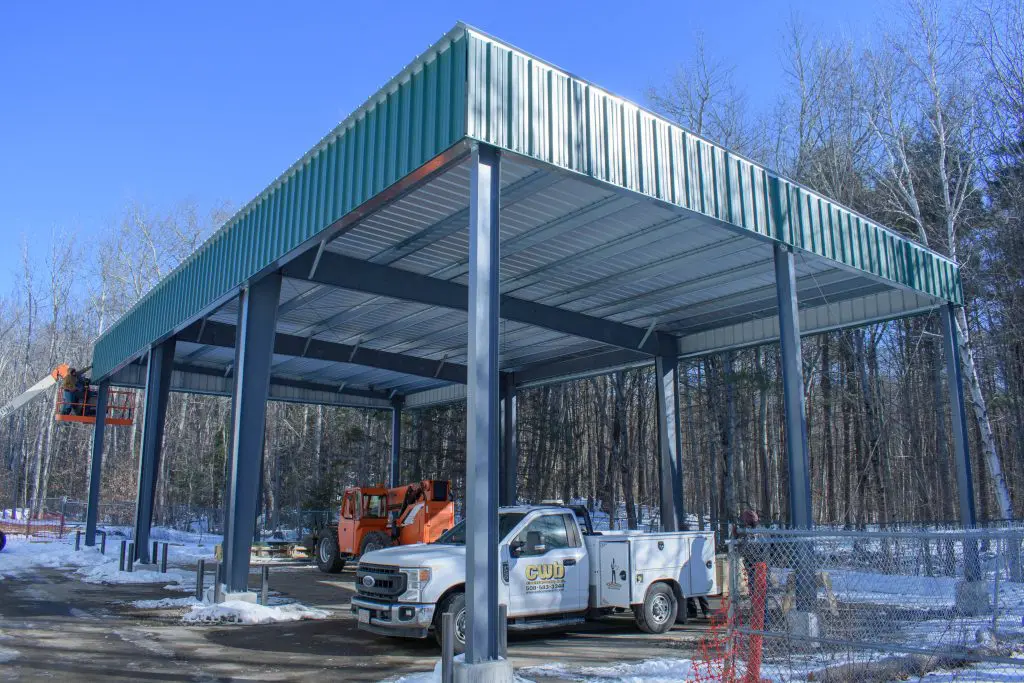
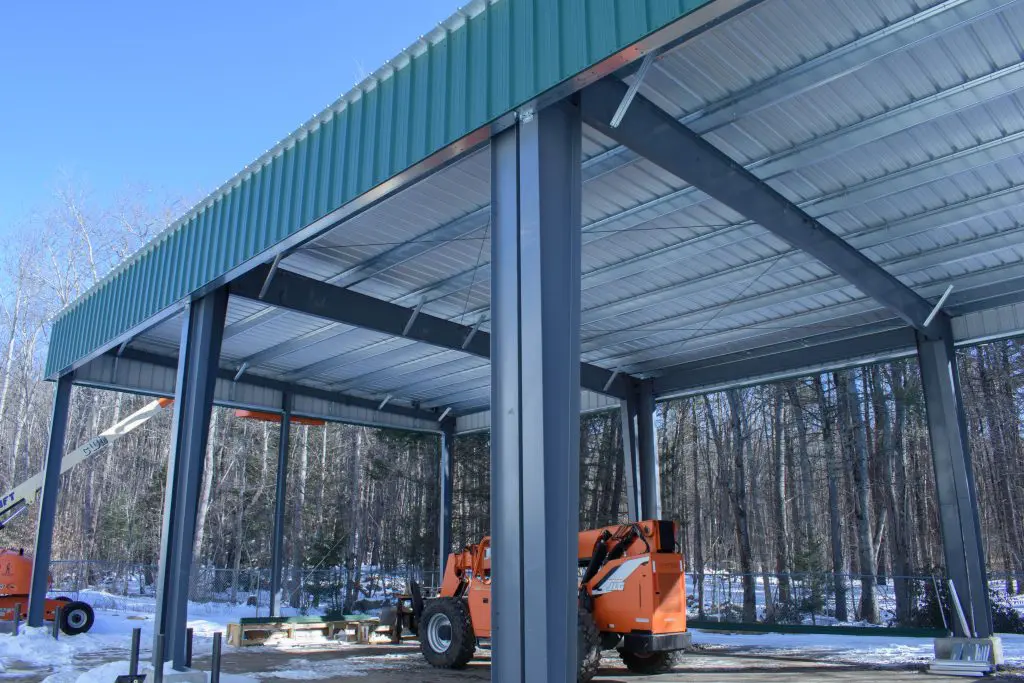
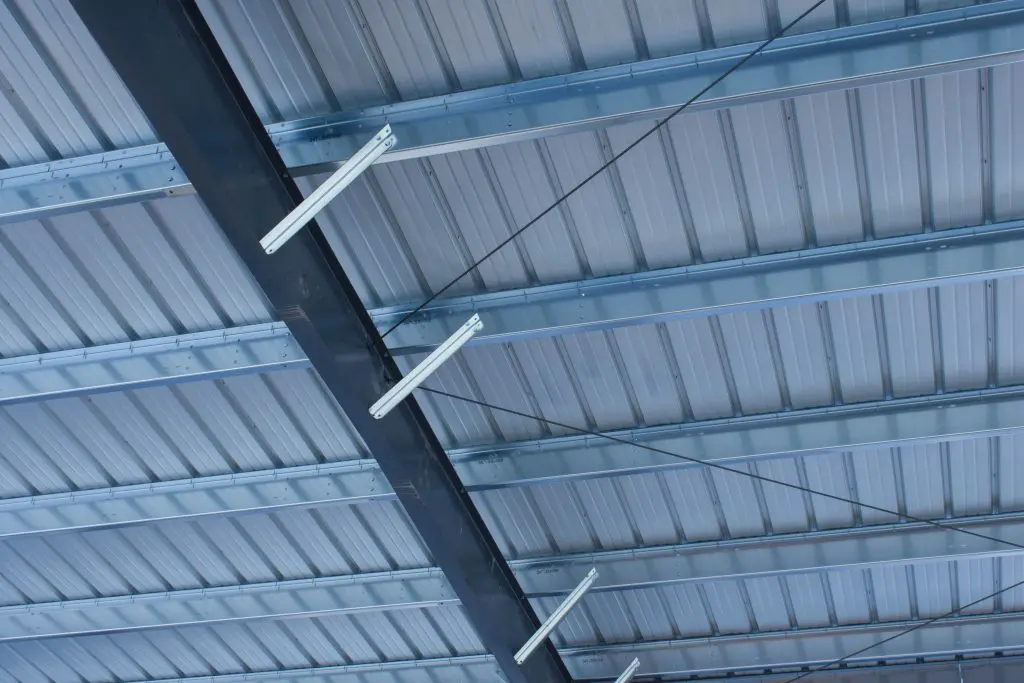
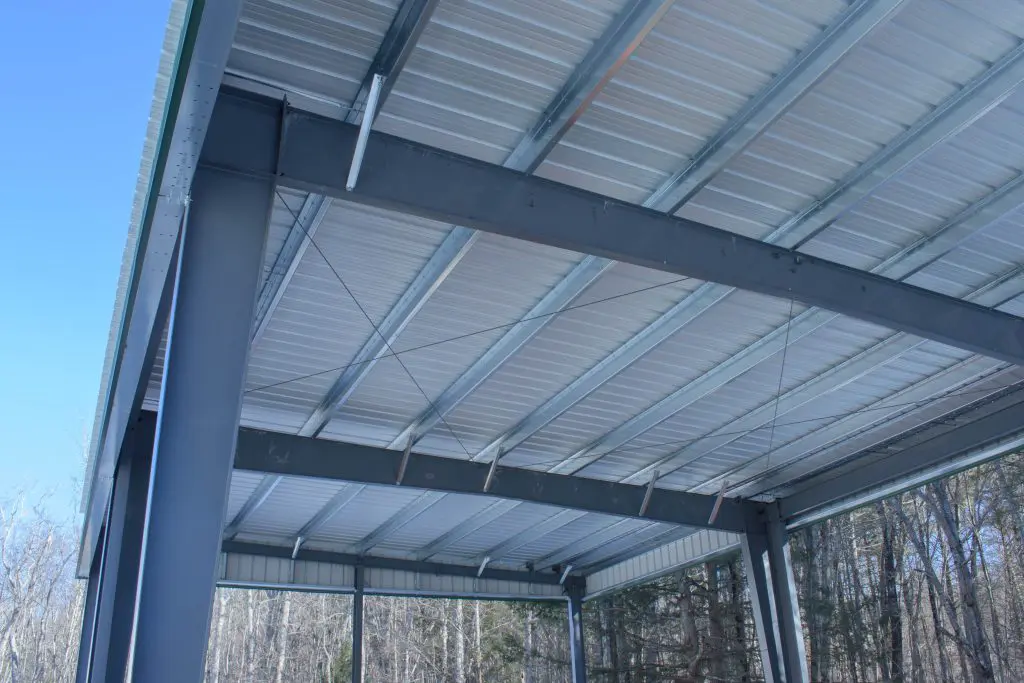
Major Products Selected
We chose industry-best solutions according to the specific needs of the project.
- Butler Pre-Engineered Metal Building
- Butler Rib screw down roof
- Butler Coat finish
- BODE Bollards
- Engineering services/solutions
- Design-Build construction